Quality Inspection
What is a Product Inspection?
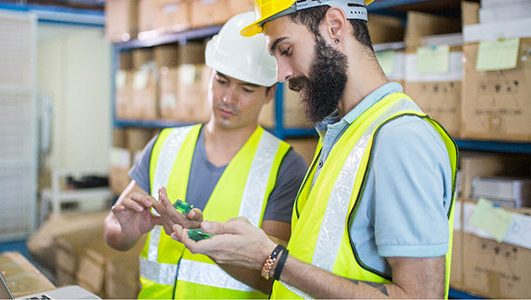
As a key element of quality control. Product inspection is where you inspect the quality of your products at different stages of the production process and before shipping. Detecting products before they ship is an effective way to prevent quality issues and supply chain disruptions.
UNISOURCE will check all the items one by one before delivery, and provide them with photos. Videos are taken throughout the loading process to ensure the loading quality of each container. We can provide pictures and videos of factory audits and on-site factory inspections.
How to Product Inspection?
STEP 1
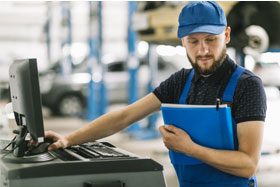
Pre-Production Inspections
Conducted before production begins, these inspections can help verify the quality of raw materials and factory readiness.
STEP 2
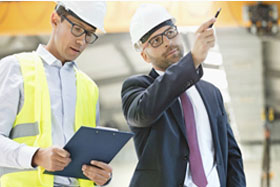
During Production Inspections
While production is still in progress. These inspections can help you detect defects early and reduce delays.
STEP 3
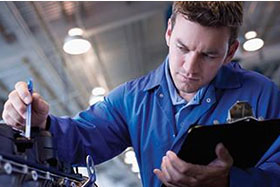
Final Random Inspections
Common types of inspections. These are carried out after your item is 100% manufactured and at least 80% packaged.
STEP 4
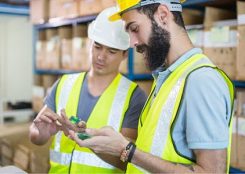
Quality inspection
One final inspection before shipping. Confirm that the product has no quality problems and then arrange for shipment.
Yes, we have a professional inspection team with a total of 6 persons. They have rich experience in goods inspection, each person inspects more than 50 items every day.
1. Measure the size and weight of each carton.
2. Check if the carton is strong and the shipping mark is correct. In the meanwhile we take photos of the carton.
3. Check if the quantity is correct after open the carton, and take photos.
4. Check the products according to the requirements of customers, and take photos of the goods.
5.If some function items,we will also test it and make sure everything is OK.
Beside the professional inspection team to check the products in warehouse, we also have at least two staffs in the office to check all the inspection pictures again to ensure that all the goods are ok.
We will check carefully if the package, size, color and weight of the products are in accordance with the requirements of the order.
If it is a product for using such as electrical products, the voltage of 220V ones we will plug in electricity to test and put it back if it is qualified.
Besides, we will ask the inspection team to take one sample of each item to the office if the customer allows, to re-check each product according to the customer’s requirements.
Usually it is about 20% .If the customer has special requirements such as full inspection, we will follow customer request. But we need charge additional costs according to the order situation.
We will communicate with the factory on behalf of the customer first. So that we can see if factory can do the order again according to the customer’s requirements or make a change/correction.
If not, we will try to get a discount for our customers.
And truthfully give the feedback to the customers, the customers will make the final decision.
WHY UNISOURCE
- Wide range of products at competitive prices
- Free warehousing for 30 days, consolidate goods from different suppliers
- Complete product design repackaging service
- Provide personalized one-stop solutions for supermarkets, retailers, wholesalers, etc.
- good after-sales service
Sourcing Agent in Yiwu China Blogs
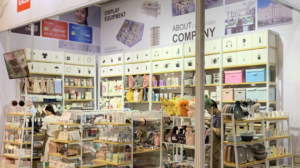
Yiwu Small Commodity Wholesale Market Gloves Industry is Prosperous in Domestic Sales
The price of gloves in the Yiwu Small Commodity Wholesale Market has been stable. Among them, the price of labor insurance gloves has dropped recently, and the
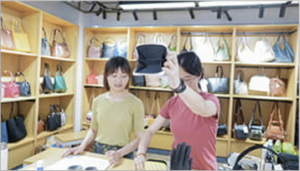
China Products Sourcing Guide
Summary: This article gives a guide on how to buy products from china. It talks about how to find high profit margin products, how to find a
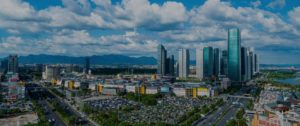
Yiwu International Trade City Skin Care and Beauty Supplies Hot Selling
As the we Welcome to WordPress. This is your first post. Edit or delete it, then start writing!